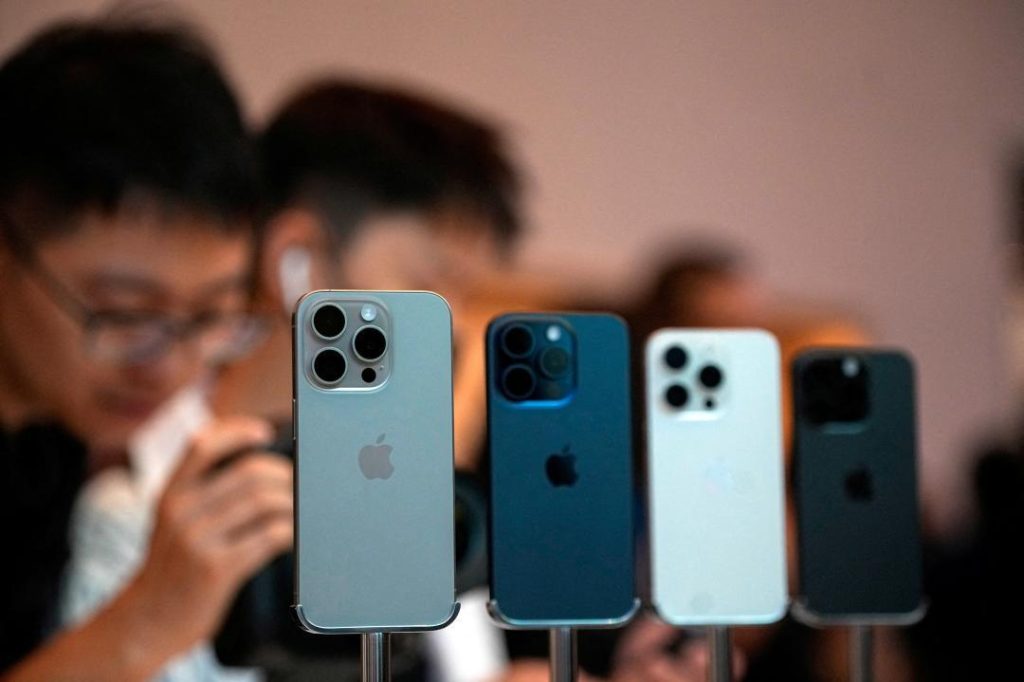
How Much Does it Cost to Make an iPhone? And How May it Change Due to US Tariffs?
The iPhone has become an iconic symbol of modern technology, with millions of people around the world relying on it for their daily communication, entertainment, and productivity needs. But have you ever wondered how much it actually costs Apple to make one of these sleek and sophisticated devices? In this blog post, we’ll delve into the costs involved in manufacturing an iPhone and how US tariffs may impact the price of these popular smartphones.
As reported by Moneycontrol, Apple spends around $580 (approximately ₹50,000) to make a 256GB iPhone 16 Pro. This cost breakdown includes several key components, such as:
- $90.85 for the A18 Pro chip: This is the brain of the iPhone, responsible for processing information and executing tasks.
- $126.95 for the rear camera system: The iPhone’s camera system is one of its most impressive features, with multiple lenses and advanced software capabilities.
- $37.97 for the display: The iPhone’s display is one of its most prominent features, with a high-resolution screen that provides crystal-clear visuals.
These costs are just a small part of the overall manufacturing process, which also includes materials, labor, and other expenses. However, they give us a sense of the scale and complexity involved in creating an iPhone.
Now, let’s consider the impact of US tariffs on iPhone manufacturing costs. As many iPhones are assembled in China, the US government’s 54% tariffs would apply to the entire manufacturing cost. This would raise the manufacturing cost of an iPhone to around $847 (approximately ₹73,400).
To put this in perspective, the average price of an iPhone 16 Pro in India is around ₹1,22,000. If the US tariffs were to be applied, the price of the iPhone could increase by as much as 15-20% in India, making it even more expensive for consumers.
But why are US tariffs relevant to iPhone manufacturing costs? In 2018, the US government imposed tariffs on a range of Chinese goods, including electronics and components. These tariffs were intended to pressure China into making concessions on trade and intellectual property issues. However, they have had a significant impact on the global technology industry, including Apple.
Apple has been vocal about its opposition to the tariffs, arguing that they will increase costs and lead to job losses. In a statement, Apple said: “We are concerned that these tariffs will increase costs for our customers and limit innovation in the technology industry.”
So, what can we expect from the future of iPhone manufacturing costs? While it’s difficult to predict exactly how US tariffs will impact the price of iPhones, it’s clear that they will have a significant impact on the industry.
In the short term, Apple may try to absorb some of the costs associated with the tariffs, passing them on to consumers in the form of increased prices. However, this could lead to a decline in demand for iPhones and other Apple products.
In the long term, Apple may look to diversify its manufacturing operations, setting up production facilities in countries with lower tariffs or more favorable trade agreements. This could help to reduce its reliance on Chinese manufacturing and mitigate the impact of US tariffs.
In conclusion, the cost of making an iPhone is a complex and multifaceted issue, influenced by a range of factors including component costs, manufacturing processes, and global trade policies. While US tariffs may increase the cost of manufacturing iPhones, Apple is likely to adapt and find ways to mitigate the impact on its customers. As technology continues to evolve and new innovations emerge, it will be fascinating to see how the iPhone and other smartphones continue to shape our world.