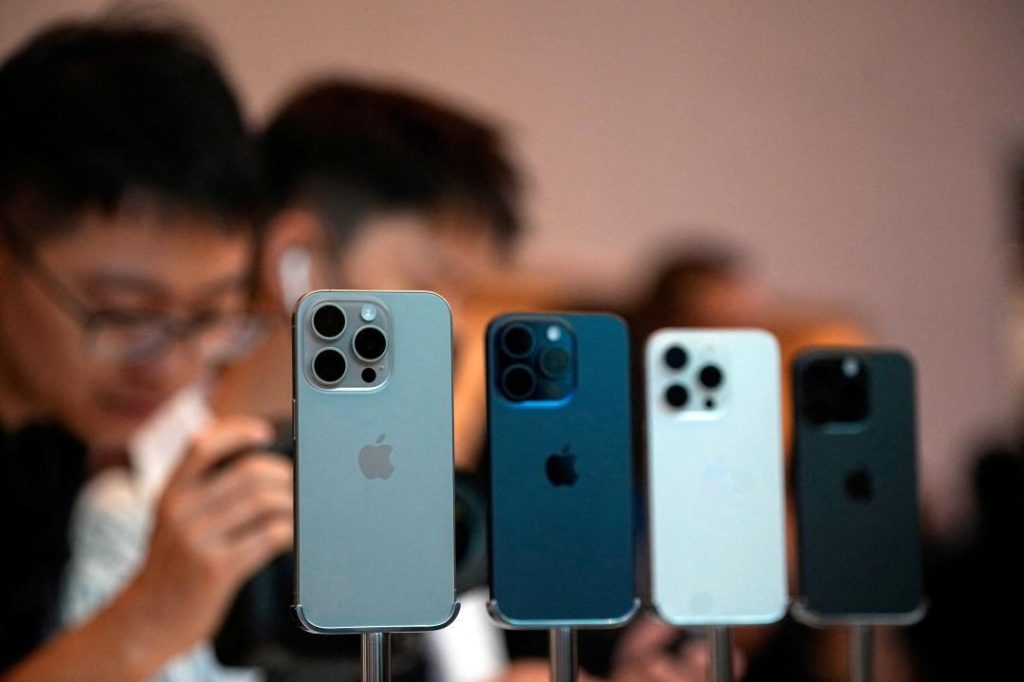
How Much Does it Cost to Make an iPhone and How May it Change Due to US Tariffs?
The iPhone is one of the most popular and sought-after smartphones in the world, with millions of units sold every quarter. But have you ever wondered how much it costs Apple to make one of these sleek devices? The answer might surprise you. According to a recent report, Apple spends around $580 (over ₹50,000) to make a 256GB iPhone 16 Pro. This cost includes various components such as the A18 Pro chip, rear camera systems, and the display.
In this blog post, we’ll take a closer look at the cost breakdown of an iPhone and how the recent US tariffs imposed on Chinese goods could impact the manufacturing cost of these devices.
Cost Breakdown of an iPhone
The cost breakdown of an iPhone varies depending on the model, storage capacity, and other factors. However, according to a report by MacRumors, the cost of an iPhone 16 Pro with 256GB storage is around $580. This cost includes the following components:
- A18 Pro Chip: $90.85
- Rear Camera Systems: $126.95
- Display: $37.97
- Other components: $325.23
As you can see, the A18 Pro chip accounts for the largest chunk of the cost, followed by the rear camera systems and display. The other components, which include the battery, memory, and other miscellaneous parts, make up the remaining 56% of the cost.
Impact of US Tariffs on iPhone Manufacturing Cost
The iPhone is assembled in China, which means it is subject to US tariffs imposed on Chinese goods. As of now, the US has imposed a 54% tariff on Chinese goods, which would apply to the entire manufacturing cost of an iPhone. This means that the manufacturing cost of an iPhone would increase to around $847 (around ₹73,400) if the tariffs are applied.
This increase in cost would have a significant impact on Apple’s profit margins, as the company would need to absorb the increased cost or pass it on to consumers. If Apple were to pass on the increased cost to consumers, it could lead to a price hike of around 45% for the iPhone 16 Pro.
Other Factors Affecting iPhone Manufacturing Cost
While the US tariffs are a significant factor in the iPhone manufacturing cost, there are other factors that also contribute to the overall cost. Some of these factors include:
- Component costs: The cost of components such as the A18 Pro chip, memory, and display can fluctuate depending on various factors such as supply and demand, production costs, and global economic conditions.
- Labor costs: The cost of labor in China, where the iPhone is assembled, can also impact the manufacturing cost. As labor costs increase, Apple may need to adjust its manufacturing process or pass on the increased cost to consumers.
- Research and development costs: Apple invests heavily in research and development to create new and innovative technologies. These costs are factored into the overall cost of the iPhone.
- Marketing and distribution costs: Apple also spends a significant amount on marketing and distribution, which includes advertising, promotions, and retail store operations. These costs are factored into the overall cost of the iPhone.
Conclusion
In conclusion, the cost of making an iPhone is complex and involves various factors such as component costs, labor costs, research and development costs, and marketing and distribution costs. While the US tariffs imposed on Chinese goods are a significant factor in the iPhone manufacturing cost, there are other factors that also contribute to the overall cost.
As the global economy continues to evolve, it’s likely that the cost of making an iPhone will continue to fluctuate. However, one thing is certain – the iPhone remains one of the most popular and sought-after smartphones in the world, and Apple will continue to invest heavily in research and development to create new and innovative technologies.
Source: