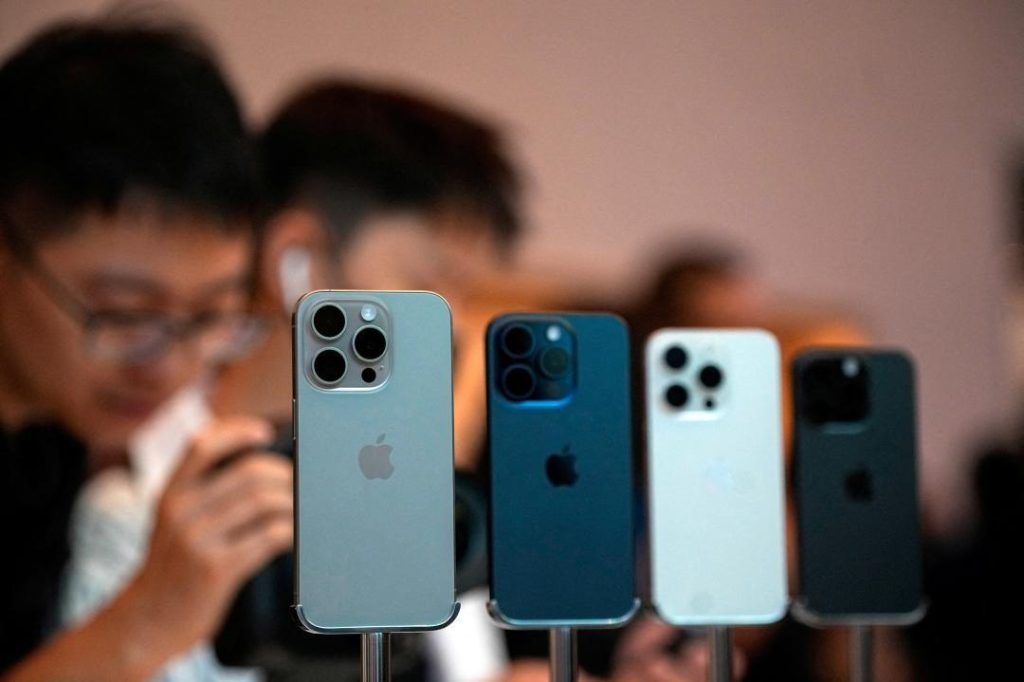
How much does it cost to make an iPhone & how may it change due to US tariffs?
The iPhone, one of the most popular and iconic smartphones in the world, is a marvel of engineering and design. But have you ever wondered how much it actually costs Apple to make one of these devices? The answer might surprise you. In a recent article, Moneycontrol revealed that Apple spends around $580 (over ₹50,000) to manufacture a 256GB iPhone 16 Pro. But what’s even more interesting is how US tariffs could potentially increase this cost.
So, where does Apple spend its money? According to the article, the breakdown of the costs is as follows:
- $90.85 for an A18 Pro chip
- $126.95 for rear camera systems
- $37.97 for the display
- Other components, including batteries, storage, and casing, account for the remaining $325.23
This total cost of $580 is the average cost for a 256GB iPhone 16 Pro, but it’s worth noting that prices can vary depending on the specific model, storage capacity, and other factors.
Now, here’s where US tariffs come in. Since many iPhones are assembled in China, US tariffs of 54% would apply to the entire manufacturing cost. This would raise the cost of production to around $847 (around ₹73,400). This is a significant increase, and it’s no wonder that Apple has been vocal about its concerns over the tariffs.
But why should we care about the cost of making an iPhone? Well, for starters, it has a direct impact on the prices consumers pay for these devices. If Apple’s costs increase, it’s likely that prices will rise too. This could have a significant impact on consumers, especially in countries where smartphones are a vital part of daily life.
Moreover, the cost of making an iPhone also has broader implications for the global economy. The iPhone is a global supply chain behemoth, with components sourced from all over the world. Tariffs on these components could cause a ripple effect throughout the entire supply chain, leading to increased costs and potentially even job losses.
So, what does this mean for Apple and its customers? Well, Apple has already announced plans to absorb some of the costs of the tariffs, but it’s unclear how much of the burden it will be able to pass on to consumers. In the short term, this could lead to higher prices for certain iPhone models. In the long term, Apple may need to consider alternative manufacturing locations or supply chain strategies to mitigate the impact of tariffs.
For consumers, this could mean that the next time you’re in the market for a new iPhone, you may need to pay a bit more. However, it’s worth noting that Apple has a reputation for being a premium brand, and its products often come with a higher price tag. Whether or not the increased cost is justified will depend on individual consumers and their willingness to pay for the latest and greatest technology.
In conclusion, the cost of making an iPhone is a complex and multifaceted issue, influenced by a variety of factors including tariffs, manufacturing costs, and supply chain dynamics. While the prospect of higher prices may be unsettling for consumers, it’s also a reminder of the global nature of the economy and the interconnectedness of supply chains. As we navigate the complex landscape of tariffs and global trade, it’s essential to stay informed and adapt to changing circumstances.