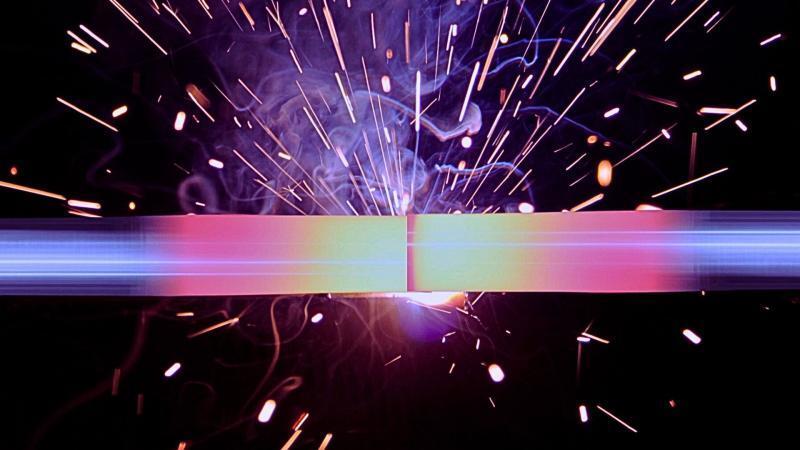
Innovation in Welding Techniques: A Game-Changer for Dissimilar Metal Applications
Welding is a widely used technique in various industries, including aerospace, automotive, and construction, to join two metal parts together. The process involves applying heat and pressure to melt the metals and fuse them together. However, traditional welding techniques often face challenges when working with dissimilar metals, which can result in weak joints and reduced structural integrity.
Recently, researchers from IIT Bombay have made a breakthrough in welding technology by developing a novel methodology that enhances rotary friction welding by altering the interface geometry. By implementing a tapered design on the titanium rod, they have successfully retained a thicker nickel interlayer, preventing brittle intermetallic formations at the weld interface.
This innovation has significant implications for industries that rely on welding dissimilar metals, such as aerospace and automotive. In this blog post, we will delve into the details of this research and explore the benefits of this novel welding technique.
The Challenge of Welding Dissimilar Metals
Welding dissimilar metals is a complex process that requires careful consideration of the materials’ properties, thermal expansion, and contraction. When two metals with different thermal expansion coefficients are joined, the joint can be prone to cracking and failure. Additionally, the formation of intermetallic compounds at the weld interface can reduce the structural integrity of the joint.
Traditional welding techniques, such as gas metal arc welding (GMAW) and gas tungsten arc welding (GTAW), often struggle to produce strong and reliable joints when working with dissimilar metals. This is because these techniques rely on the formation of a strong fusion zone, which can be challenging to achieve when the metals have different melting points and thermal conductivity.
The Novel Methodology
The researchers from IIT Bombay have developed a novel methodology that enhances rotary friction welding by altering the interface geometry. Rotary friction welding is a solid-state welding process that uses rotational motion and friction to join two metals together. The process involves rotating one metal against the other while applying a high pressure to generate heat and produce a joint.
In this study, the researchers implemented a tapered design on the titanium rod, which was used as the anode in the welding process. The tapered design allowed them to retain a thicker nickel interlayer at the weld interface, which significantly improved the structural integrity of the joint.
The researchers used a combination of experimental and simulation techniques to study the welding process and optimize the parameters. They found that the tapered design allowed for a more uniform distribution of heat and pressure at the weld interface, which resulted in a stronger and more reliable joint.
Benefits of the Novel Methodology
The novel methodology developed by the IIT Bombay researchers offers several benefits over traditional welding techniques. These benefits include:
- Improved structural integrity: The tapered design allows for the retention of a thicker nickel interlayer, which prevents brittle intermetallic formations at the weld interface. This results in a stronger and more reliable joint.
- Increased weld strength: The uniform distribution of heat and pressure at the weld interface resulting from the tapered design allows for a stronger weld.
- Reduced risk of cracking: The novel methodology reduces the risk of cracking and failure at the weld interface, making it suitable for applications where reliability is critical.
- Improved weld quality: The researchers found that the tapered design resulted in a more consistent and uniform weld, which is critical for applications where high-quality welds are required.
Industrial Applications
The novel methodology developed by the IIT Bombay researchers has significant implications for industries that rely on welding dissimilar metals. Some potential applications include:
- Aerospace industry: The novel methodology could be used to join titanium and aluminum alloys, which are commonly used in aircraft and spacecraft.
- Automotive industry: The methodology could be used to join dissimilar metals in the production of engine components, such as cylinder heads and engine blocks.
- Construction industry: The novel methodology could be used to join dissimilar metals in the production of structural components, such as bridges and buildings.
Conclusion
The novel methodology developed by the IIT Bombay researchers is a significant innovation in welding technology that has the potential to revolutionize the industry. By altering the interface geometry and implementing a tapered design on the titanium rod, the researchers have successfully retained a thicker nickel interlayer, preventing brittle intermetallic formations at the weld interface.
This innovation has significant implications for industries that rely on welding dissimilar metals, and it is expected to improve the structural integrity and reliability of welds. As the demand for high-strength and lightweight materials continues to grow, this novel methodology is expected to play a critical role in the development of next-generation materials and technologies.
Source: