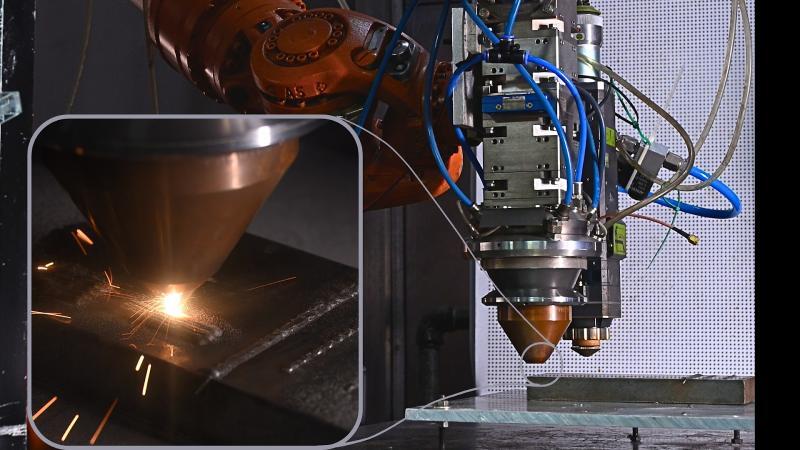
Advancing 3D Printing through In-situ Laser Remelting
The rapid growth of 3D printing technology has revolutionized the manufacturing industry, enabling the production of complex geometries and customized products with unprecedented speed and accuracy. However, there are still significant challenges to overcome, particularly when it comes to 3D printing of metals. Researchers at IIT Bombay have made a groundbreaking discovery, introducing in-situ laser remelting, a technique that enhances 3D printing speed by 2.5 times without compromising quality. This innovative approach has the potential to transform the manufacturing landscape, reducing defects, saving energy, and making India a self-reliant hub for advanced manufacturing.
The Challenge of Metal 3D Printing
Metal 3D printing, also known as additive manufacturing, is a complex process that involves layer-by-layer deposition of metal powders or wires. While this technique offers many advantages, including reduced material waste and increased design flexibility, it also presents several challenges. One of the primary concerns is the formation of defects, such as porosity and cracking, which can significantly impact the structural integrity and durability of the final product.
In-situ Laser Remelting: A Game-Changer
To address the limitations of traditional metal 3D printing, researchers at IIT Bombay have developed an innovative technique called in-situ laser remelting. This method involves remelting each layer of metal powder or wire before depositing the next layer. This process ensures that the metal is fully melted and uniform, resulting in a significant improvement in structural strength and density.
The in-situ laser remelting technique is particularly effective for printing complex geometries and thin-walled structures, where defects are more likely to occur. By remelting each layer, the researchers can eliminate porosity and cracking, ensuring that the final product has a high level of quality and reliability.
Benefits of In-situ Laser Remelting
The benefits of in-situ laser remelting are numerous and significant. Some of the key advantages include:
- Improved Structural Strength: By remelting each layer, the researchers can ensure that the metal is fully melted and uniform, resulting in a significant improvement in structural strength and density.
- Reduced Defects: In-situ laser remelting eliminates porosity and cracking, ensuring that the final product has a high level of quality and reliability.
- Increased Speed: The remelting process allows for faster printing speeds, reducing production time and increasing efficiency.
- Energy Savings: The reduced need for re-melting and re-printing layers results in significant energy savings.
- No New Machinery Required: The in-situ laser remelting technique can be integrated into existing 3D printing machines, eliminating the need for new equipment.
Potential Applications
The in-situ laser remelting technique has the potential to transform various industries, including aerospace, automotive, healthcare, and energy. Some potential applications include:
- Aerospace: In-situ laser remelting can be used to print complex aircraft components, such as jet engine parts and satellite components, with improved strength and durability.
- Automotive: The technique can be used to print car parts, such as engine blocks and cylinder heads, with reduced weight and increased strength.
- Healthcare: In-situ laser remelting can be used to print medical implants, such as hip and knee replacements, with improved biocompatibility and durability.
- Energy: The technique can be used to print energy-related components, such as wind turbine blades and solar panels, with improved efficiency and durability.
Conclusion
The introduction of in-situ laser remelting is a significant breakthrough in the field of 3D printing, particularly for metal printing. This innovative technique has the potential to transform the manufacturing landscape, reducing defects, saving energy, and making India a self-reliant hub for advanced manufacturing. As researchers continue to refine and develop this technology, we can expect to see a wide range of applications across various industries, from aerospace and automotive to healthcare and energy.
Source
https://researchmatters.in/news/iit-bombays-laser-trick-makes-3d-metal-printing-faster-and-stronger