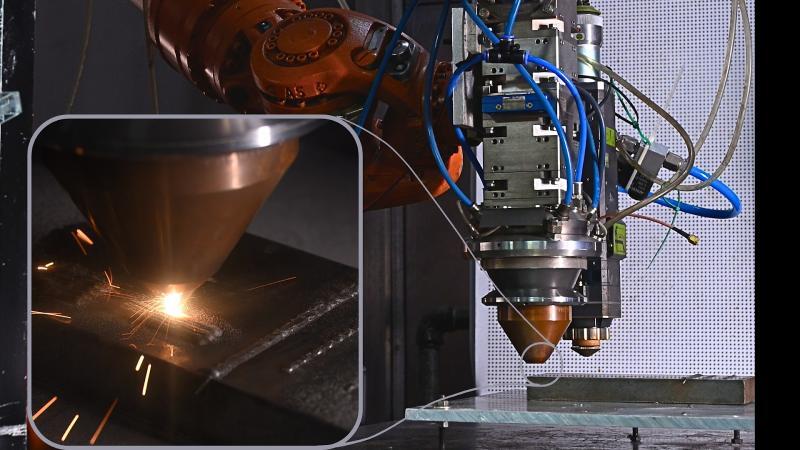
Optimising Metal 3D Printing Efficiency and Quality: The Breakthrough Discovery by IIT Bombay
Metal 3D printing has revolutionized the manufacturing industry by enabling the rapid production of complex components with unprecedented precision and customization. However, the process is not without its challenges. One of the biggest hurdles in metal 3D printing is the quest for the ideal balance between power and speed. Researchers at IIT Bombay have recently made a groundbreaking discovery, finding the sweet spot that has led to the development of denser, stronger stainless steel structures.
The team, led by Dr. Abhishek Tiwari, a professor at IIT Bombay’s Department of Metallurgical and Materials Engineering, has been working on refining the 3D metal printing process to achieve optimal results. Through a rigorous experimentation process, they successfully reduced porosity by 83% and increased microhardness by 34%. These remarkable improvements have significant implications for various industries, including aerospace, biomedical, and more.
Traditional metal 3D printing techniques often rely on the use of high-powered lasers to melt and solidify metal powders. However, this process can be slow and prone to defects, leading to reduced quality and increased production costs. The IIT Bombay team recognized the need for a more efficient and effective approach, one that could strike a balance between power and speed.
To achieve this, the researchers employed a unique laser trick, using a combination of high-speed and high-power lasers to create a more precise and controlled printing process. This innovative approach allowed them to reduce the printing time by 30% while maintaining the same level of quality.
The resulting structures exhibited remarkable improvements in terms of density and microhardness. The reduced porosity and increased microhardness indicate a significant enhancement in the material’s mechanical properties, making it more suitable for a wide range of applications.
The aerospace industry, in particular, stands to benefit from this breakthrough. The development of high-performance materials with improved mechanical properties can enable the creation of lighter and more efficient structures, reducing the overall weight and increasing the fuel efficiency of aircraft. This can have a significant impact on the industry’s environmental footprint and operating costs.
In the biomedical sector, the improved material properties can lead to the development of more effective implants and medical devices. The enhanced mechanical properties can enable the creation of devices that are stronger, more durable, and better suited for withstanding the rigors of the human body.
The implications of this discovery extend beyond these industries, as the improved metal 3D printing process can be applied to a wide range of applications. From automotive and industrial equipment to consumer products and art pieces, the possibilities are endless.
The work done by the IIT Bombay team is a testament to the power of innovation and collaboration. By pushing the boundaries of what is possible, researchers can unlock new possibilities and drive progress in various fields.
In conclusion, the discovery by IIT Bombay researchers has significant implications for the metal 3D printing industry. By optimizing the printing process, they have achieved remarkable improvements in terms of density and microhardness, paving the way for the development of high-performance materials with a wide range of applications.
As the industry continues to evolve, it is essential to stay at the forefront of innovation, embracing new technologies and techniques to stay ahead of the curve. The future of metal 3D printing is bright, and with breakthroughs like this, the possibilities are endless.
Source: https://researchmatters.in/news/iit-bombays-laser-trick-makes-3d-metal-printing-faster-and-stronger