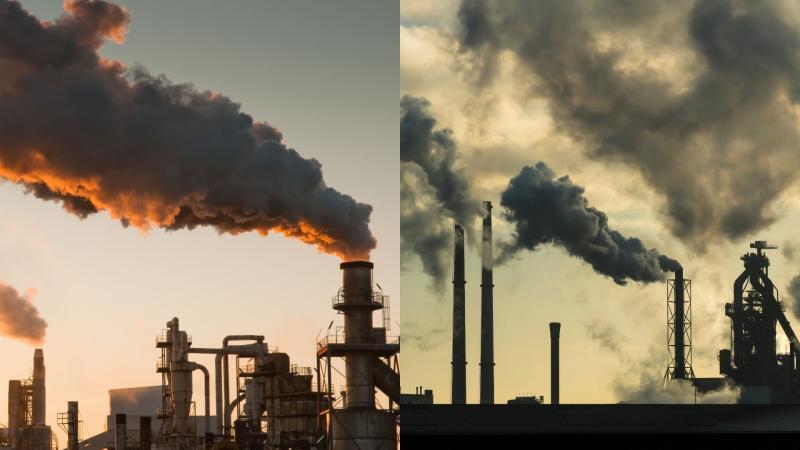
Pioneering a Sustainable Future for the Steel Industry
The steel industry is one of the most significant contributors to greenhouse gas emissions, accounting for around 7% of global CO2 emissions. The traditional method of steel production, which involves the use of coal, is a significant source of these emissions. However, researchers at IIT Bombay are working towards transforming the steel industry by utilizing hydrogen-based direct reduction instead of coal. This innovative approach, coupled with cobalt-based catalysts for water electrolysis, has the potential to significantly decrease carbon emissions.
The Problem with Traditional Steel Production
Traditional steel production involves the use of coal to reduce iron ore into steel. This process, known as blast furnace-based steel production, is energy-intensive and relies heavily on fossil fuels. As a result, it is a significant contributor to greenhouse gas emissions. The steel industry is also a major consumer of energy, accounting for around 2% of global energy consumption.
The Solution: Hydrogen-Based Direct Reduction
IIT Bombay researchers have been working on developing a more sustainable method of steel production, known as hydrogen-based direct reduction. This process involves the use of hydrogen to reduce iron ore into steel, rather than coal. This method has several advantages over traditional steel production. Firstly, it is cleaner and more environmentally friendly, as it produces no greenhouse gas emissions during the production process. Secondly, it is more energy-efficient, as it uses hydrogen rather than coal as a reducing agent.
Cobalt-Based Catalysts for Water Electrolysis
To make hydrogen-based direct reduction a reality, researchers have developed cobalt-based catalysts for water electrolysis. Water electrolysis is a process that involves the splitting of water into hydrogen and oxygen using an electric current. The cobalt-based catalysts developed by IIT Bombay researchers have been shown to increase the efficiency of this process, making it more viable for large-scale industrial applications.
Electric Arc Furnace Technology
Another critical component of the sustainable steel production process is electric arc furnace technology. Electric arc furnaces use electricity to melt scrap steel and produce new steel. This technology is more energy-efficient than traditional blast furnaces, and it also produces fewer emissions.
Carbon Capture and Storage
To further reduce the carbon footprint of steel production, researchers have also been exploring the use of carbon capture and storage technology. Carbon capture and storage involves capturing CO2 emissions from the production process and storing them underground or utilizing them in other industrial applications.
The Future of Steel Production
The development of hydrogen-based direct reduction, cobalt-based catalysts for water electrolysis, electric arc furnace technology, and carbon capture and storage has the potential to transform the steel industry. By integrating these technologies, steel production can approach carbon-neutrality, reducing the industry’s carbon footprint and contributing to a more sustainable future.
Conclusion
The steel industry is a significant contributor to greenhouse gas emissions, but it is also a critical component of modern society. The development of sustainable steel production technologies has the potential to transform the industry and help reduce its carbon footprint. IIT Bombay researchers are at the forefront of this effort, developing innovative technologies that can help reduce emissions and create a more sustainable future for the steel industry.
Source: