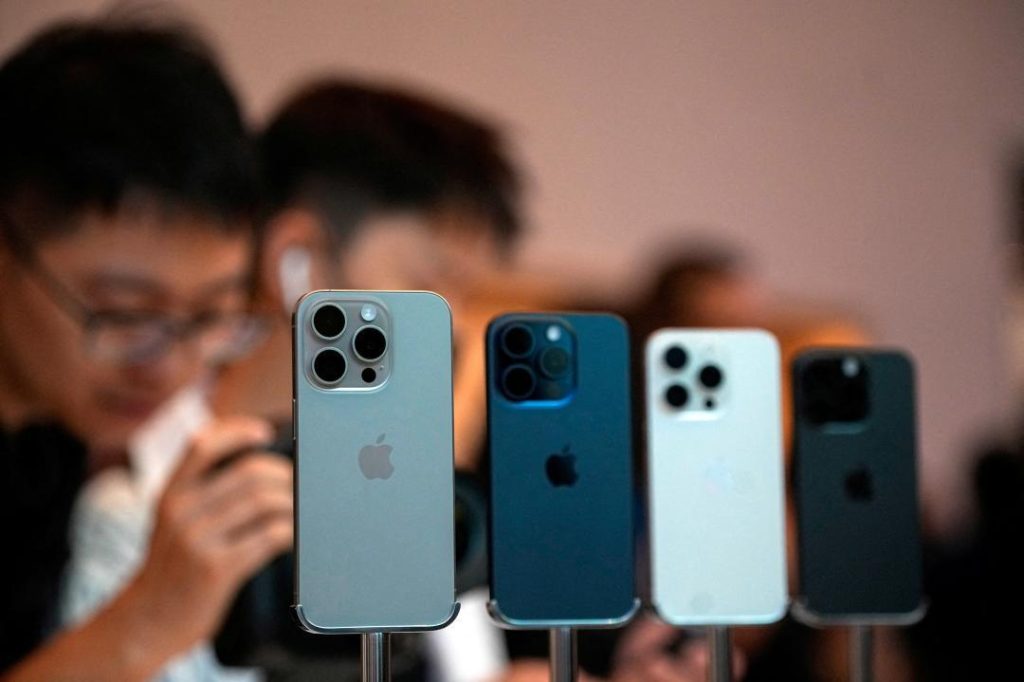
How much does it cost to make an iPhone & how may it change due to US tariffs?
The cost of making an iPhone is a closely guarded secret, but thanks to some recent revelations, we can get a glimpse into the manufacturing costs of Apple’s flagship device. According to a report by Moneycontrol, Apple spends around $580 (over ₹50,000) to make a 256GB iPhone 16 Pro. This cost includes various components such as the A18 Pro chip, rear camera systems, and the display.
Breaking down the cost
The report highlights the cost of each component, giving us an idea of where Apple’s expenses are going. Here’s a breakdown:
- A18 Pro chip: $90.85
- Rear camera systems: $126.95
- Display: $37.97
- Other components: $325.23
- Labor and manufacturing overheads: $19.00
These costs add up to a total of $580, which is the cost of making a 256GB iPhone 16 Pro. However, this cost may increase significantly due to US tariffs.
US tariffs and their impact
The US has imposed 54% tariffs on Chinese imports, including those used in the manufacturing of iPhones. As many iPhones are assembled in China, these tariffs would apply to the entire manufacturing cost of the device. This would raise the manufacturing cost of iPhones to around $847 (around ₹73,400).
The tariffs would increase the cost of components such as the A18 Pro chip, rear camera systems, and display, which are all made in China. The labor and manufacturing overheads would also be affected, leading to a significant increase in the overall cost of production.
Impact on consumers
The increased cost of production would likely be passed on to consumers, making iPhones more expensive. This could have a significant impact on Apple’s sales and profitability, particularly in countries like the US, China, and India, which are major markets for the company.
What does this mean for Apple?
Apple has been trying to mitigate the impact of tariffs by diversifying its supply chain and reducing its dependence on Chinese imports. The company has been investing in manufacturing facilities in countries like India, Vietnam, and the US, which could help reduce its exposure to tariffs.
However, the impact of tariffs on Apple’s supply chain and profitability would be significant. The company would need to find ways to absorb the increased costs or pass them on to consumers, which could affect its competitiveness in the market.
Conclusion
The cost of making an iPhone is a complex and multifaceted issue, influenced by various factors such as component prices, labor costs, and tariffs. The recent revelations about Apple’s manufacturing costs provide a glimpse into the company’s expenses and highlight the potential impact of US tariffs on its supply chain and profitability.
As the trade tensions between the US and China continue to escalate, it’s likely that the cost of making an iPhone will remain under pressure. Apple will need to continue to diversify its supply chain and find ways to reduce its dependence on Chinese imports to mitigate the impact of tariffs.
Source