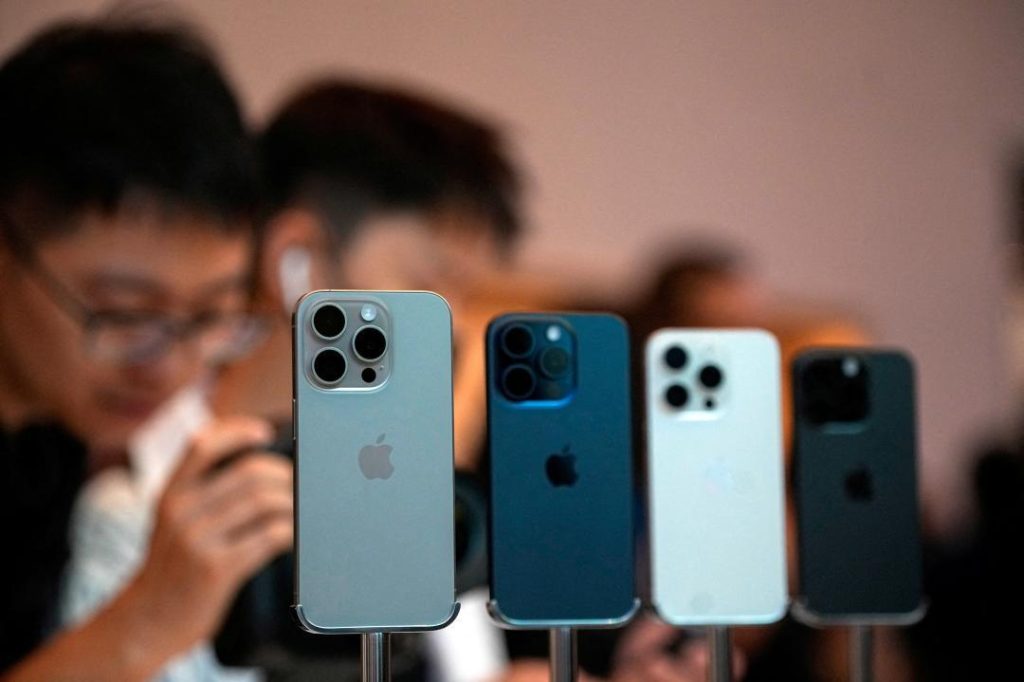
How much does it cost to make an iPhone & how may it change due to US tariffs?
The latest flagship iPhone 16 Pro has taken the world by storm, with its stunning features, sleek design, and unparalleled performance. But have you ever wondered what goes into making such an iconic device? The answer lies in the manufacturing cost of the iPhone. A recent report by Moneycontrol sheds light on the exact cost of making an iPhone, and it’s an eye-opener.
According to the report, Apple spends around $580 (over ₹50,000) to make a 256GB iPhone 16 Pro. This staggering figure may seem high, but it breaks down into some surprising components. The A18 Pro chip, which is the brain of the iPhone, costs Apple $90.85. The rear camera systems, which are a major highlight of the iPhone 16 Pro, cost a whopping $126.95. And the display, which is arguably the most critical component of any smartphone, costs $37.97.
But what happens when the iPhone is assembled in China, a country subject to US tariffs? That’s where things get interesting. Since the iPhone is assembled in China, the 54% tariffs imposed by the US government would apply to the entire manufacturing cost of the iPhone. This means that the cost of making an iPhone would jump to around $847 (approximately ₹73,400).
To put this into perspective, the iPhone 16 Pro was launched in India at a price of ₹1,29,900 for the base variant. This means that the cost of making an iPhone would account for around 64% of its retail price. This is a significant chunk, and it highlights the impact that tariffs can have on the cost of goods.
But why do tariffs matter? Tariffs are taxes imposed by governments on imported goods, and they can have a significant impact on the cost of production. In the case of the iPhone, the 54% tariffs imposed by the US government would not only increase the cost of manufacturing but also make it more difficult for Apple to compete with rival smartphone manufacturers.
So, what does this mean for Apple and its customers? For Apple, it means that the company would need to absorb the increased cost of production or pass it on to consumers. Both options have significant implications for the company. If Apple absorbs the cost, it would eat into its profit margins, making it more challenging for the company to invest in research and development, marketing, and other areas. On the other hand, if Apple passes on the cost to consumers, it would increase the retail price of the iPhone, making it less competitive in the market.
For customers, it means that the prices of iPhones could increase significantly. In an already competitive market, this could make it more challenging for Apple to maintain its market share. It could also lead to a shift in consumer behavior, with customers opting for cheaper alternatives or waiting for prices to come down.
But it’s not all doom and gloom. For Apple, the tariffs could also present an opportunity to re-evaluate its supply chain and manufacturing strategy. With the threat of tariffs looming, Apple might consider diversifying its manufacturing base to countries like India, Vietnam, or Taiwan. This could not only reduce its reliance on China but also provide a more stable and cost-effective supply chain.
In conclusion, the cost of making an iPhone is a complex and multifaceted issue. While the exact figure of $580 might seem high, it’s a testament to the level of engineering, design, and manufacturing expertise that goes into creating such a device. However, the impact of tariffs on the cost of production is a significant concern, and it’s one that Apple and its customers will need to grapple with in the coming months.