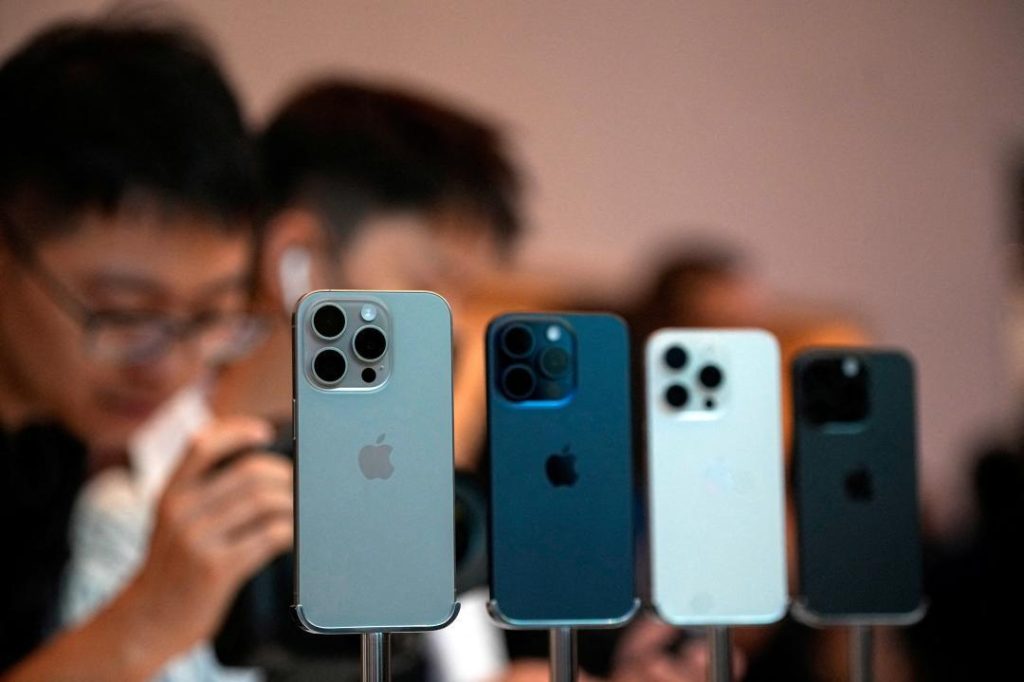
How Much Does It Cost to Make an iPhone? And How May It Change Due to US Tariffs?
The iPhone is one of the most iconic and sought-after smartphones in the world, with millions of units sold every quarter. But have you ever wondered how much it costs Apple to make an iPhone? The answer might surprise you. In this blog post, we’ll delve into the breakdown of the costs involved in manufacturing an iPhone and explore how the recent US tariffs could impact its price.
According to a recent report by Moneycontrol, Apple spends approximately $580 (over ₹50,000) to make a 256GB iPhone 16 Pro. This staggering figure includes various components and manufacturing costs. Let’s break down the costs to understand where the money goes:
-
A18 Pro Chip: $90.85
The brain of the iPhone, the A18 Pro chip, is the most expensive component, accounting for around 16% of the total manufacturing cost. This high-performance chip is responsible for processing the phone’s advanced features, such as artificial intelligence, machine learning, and graphics rendering. -
Rear Camera Systems: $126.95
The camera system is another critical component, taking up around 22% of the total cost. The iPhone 16 Pro features a quad-camera setup with a high-resolution primary sensor, telephoto lens, ultra-wide-angle lens, and a time-of-flight camera. The cost of these cameras, lenses, and image processing components adds up quickly. -
Display: $37.97
The display is another significant expense, accounting for around 7% of the total cost. The iPhone 16 Pro features a 6.1-inch Super Retina XDR OLED display with a Quad HD+ resolution, which requires high-quality OLED panels, touch sensors, and other components. -
Other Components and Manufacturing Costs: $325.23
The remaining costs include various components such as memory, storage, batteries, and other peripherals, as well as manufacturing expenses like labor, overhead, and research and development.
As you can see, the cost of manufacturing an iPhone is substantial, but it’s still a fraction of the device’s retail price. The iPhone 16 Pro, for instance, starts at around $999 (around ₹87,000) for the base model.
However, with the recent imposition of US tariffs on Chinese goods, the cost of manufacturing an iPhone could increase significantly. The US has imposed a 54% tariff on Chinese goods, including those used in the production of iPhones. This means that Apple would need to pay an additional 54% on the entire manufacturing cost of an iPhone.
Using the same example as above, the total manufacturing cost of an iPhone 16 Pro would increase to around $847 (around ₹73,400). This would put a significant strain on Apple’s profit margins, potentially leading to increased prices for consumers.
The Impact of US Tariffs on iPhone Prices
The imposition of US tariffs on Chinese goods could have a ripple effect on the global smartphone market. Apple, being a major importer of Chinese components, would need to absorb the additional costs or pass them on to consumers. This could lead to a range of outcomes:
- Price Increases: Apple might increase the prices of iPhones to maintain its profit margins, making them less competitive in the market.
- Reduced Profit Margins: Apple might choose to maintain the current prices and absorb the additional costs, reducing its profit margins.
- Supply Chain Disruptions: The tariffs could disrupt the global supply chain, leading to component shortages and production delays.
- Increased Competition: Other smartphone manufacturers might take advantage of the situation and offer more competitive pricing, potentially eating into Apple’s market share.
Conclusion
The cost of manufacturing an iPhone is complex and involves various components and manufacturing costs. While the recent US tariffs on Chinese goods could increase the cost of production, Apple might need to find ways to absorb these costs or pass them on to consumers. As the global smartphone market continues to evolve, it’s essential to monitor the impact of tariffs on the industry and the potential effects on consumers.
Sources: